Following new, more stringent Tier IV diesel engine emissions regulations, Rayco, an environmental equipment designer for the tree care and landscape industries, took the opportunity to develop a more efficient, powerful and compact stump cutter, the RG165T-R.
In comparison to previous designs that utilized diesel engines, Rayco’s new stump cutter is centered around a powerful 165 HP gasoline engine.
As a result of the new gasoline design, the equipment’s envelope size was reduced and components were eliminated, such as after-treatment systems, diesel exhaust fluid, and electronics. In addition to the robust gasoline engine, the RG 165T-R also packs a closed-circuit hydrostatic cutter wheel drive system that delivers full engine HP to the cutter wheel, completing every job in its path.
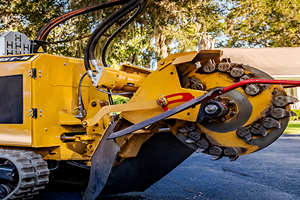
Stump cutting presents unique operating scenarios with each cycle. A pump and motor must be able to power through different obstacles at each job site. From technical support to high-quality hydraulic components to quick, on-time delivery, Parker enabled Rayco to develop its new industry-leading stump cutter.
The initial RG165T-R prototype was created using the Parker Series F12 182cc bent axis motor, along with a competitor’s 90cc closed circuit pump. However, during initial rounds of testing, the competitor’s 90cc closed circuit pump struggled with performance and reliability issues, along with the potential for long lead times.
When Rayco reached out to the Parker applications team, they recommended an alternative – the compact, high-performance C Series 81cc hydrostat piston pump and promptly delivered a unit for testing. During subsequent testing of the Parker pump and motor combination, the team worked with Rayco engineers to dial in the performance.
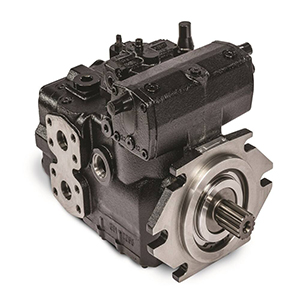
By incorporating these two Parker components, Rayco engineers were able to exceed multiple performance targets. These targets included a 20 percent decrease in heat generation while increasing system efficiency by 10 percent over alternative test units. The C Series pump delivered excellent power density and paired perfectly with the 182cc F12 motor. The combination also translated into the optimal cutter wheel speed, which increased torque output to the cutter teeth by 10%. Another and unexpected benefit of the system was a tighter radius of the wood chips to the machine, resulting in less operational risk during the stump grinding process.
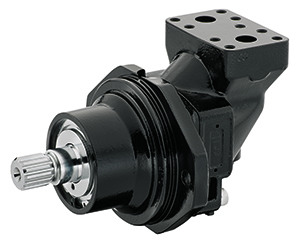
Parker’s Hydraulic Pump and Power Systems Division has been designing pumps and transmission for over 50 years. The division is the result of the Parker piston pump business’s acquisition of Denison Hydraulics and the merger with the Parker Oildyne Division. These two businesses combined have extended Parker’s product offering to include the quality compact hydraulic products and systems the division has been pioneering since 1955.
This article was contributed by Justin Wheeler, product manager, and Wes Jackson, application engineer for Parker Hannifin’s Hydraulic Pump and Power Systems Division. Licensing for the images came with permission from the Parker Hannifin Media Manager collection.
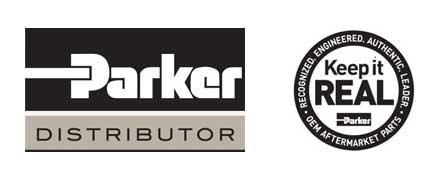