Hydraulic contamination causes up to 70% of hydraulic system failures, making it a key challenges in fluid power management. But how do contaminants form, infiltrate hydraulic systems, and lead to such widespread failure?
In this article—reproduced with kind permission from IKRON Fluid Filtration—we explore the primary hydraulic contamination causes, uncovering how particulate, liquid, and gaseous contaminants enter systems and impact performance.
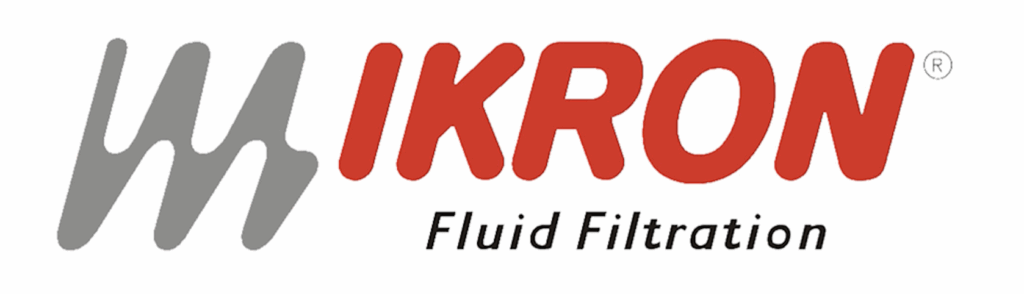
How Contaminants Form in Hydraulic Systems
Abrasion
Fluid particles, traveling at high velocity, collide with solid surfaces, scraping off material. The detached particles circulate within the system, further contributing to hydraulic contamination causes.
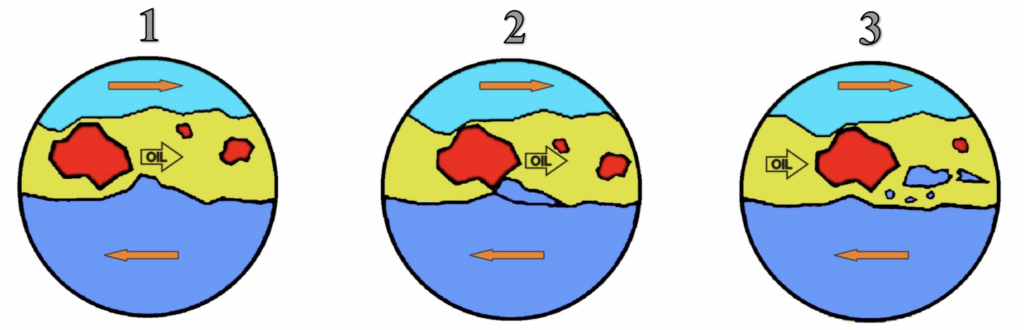
Erosion
Similar to abrasion, erosion occurs when fluid particles strike surfaces forcefully, wearing them down. As system pressure increases, microscopic fragments break away, adding to contamination levels.
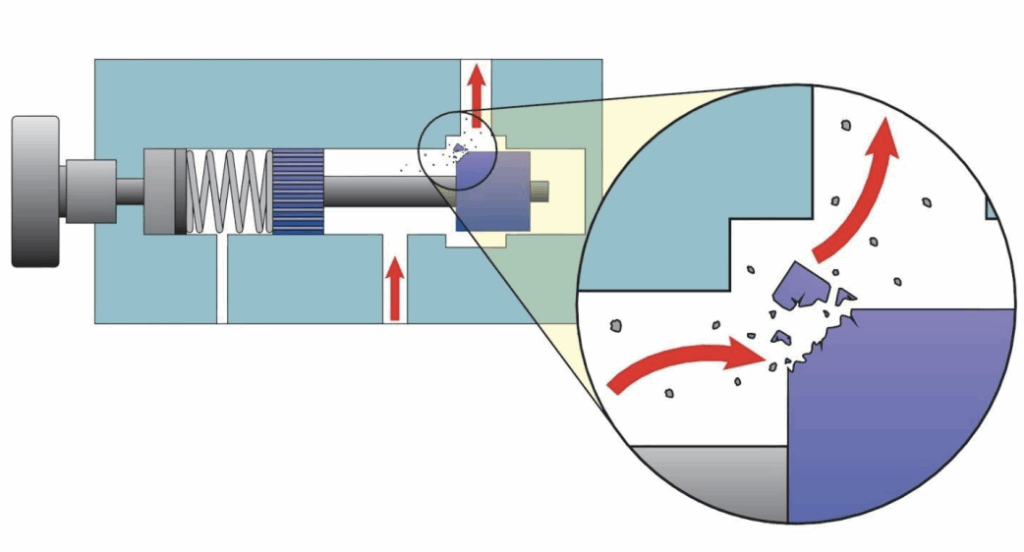
Adhesion
When metal components make contact, molecular attraction causes particles to bond together or stick to surfaces. Intense force can dislodge adhered materials, releasing contaminants into the fluid.
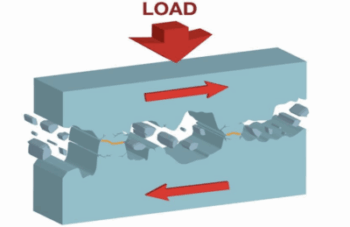
Surface Fatigue
Repeated particle impacts create microcracks, increasing surface roughness and fatigue sensitivity. Over time, mechanical stress dislodges material, intensifying contamination.
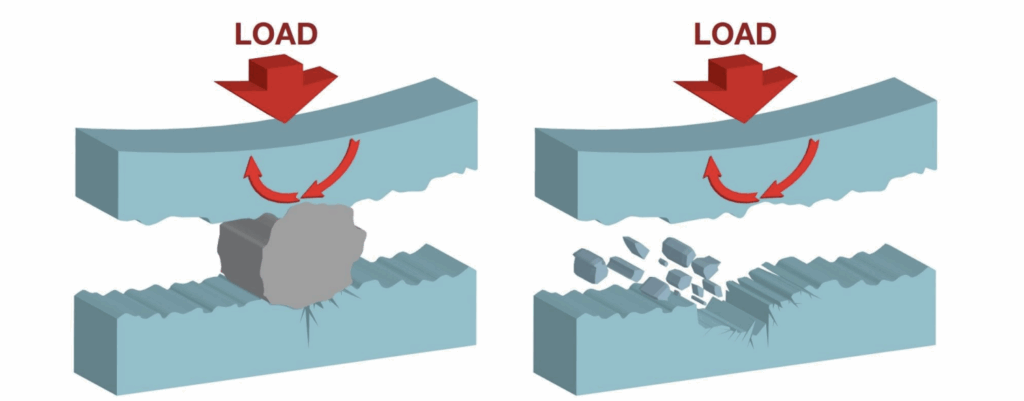
Cavitation
During the suction phase, water present in hydraulic fluid vaporizes, forming air bubbles.
As fluid transitions from low to high pressure, these bubbles collapse against metal surfaces, causing erosion and contaminant release.
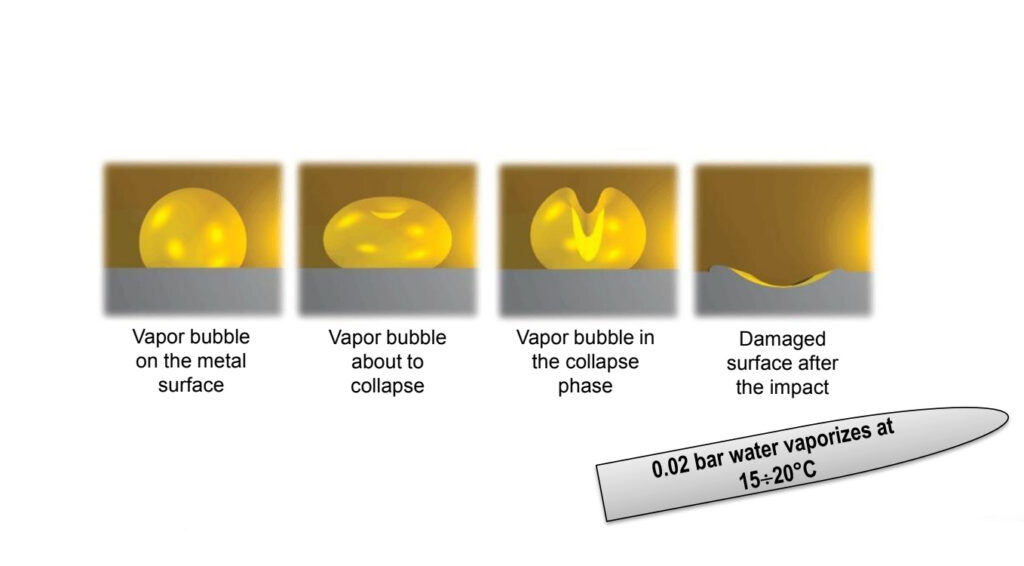
Corrosion
Water exposure accelerates oxidation, leading to rust formation. As rust deteriorates, it fractures and disperses into the fluid, increasing contamination risks.
Microbial Growth
Moist environments promote rapid microorganism reproduction, degrading fluid properties and causing further corrosion within system components.
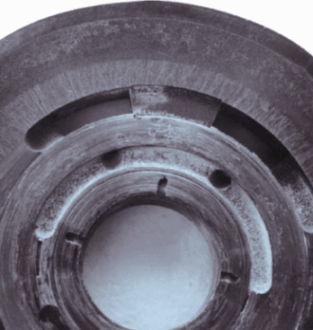
Understanding Contaminant Measurement in Hydraulics
Hydraulic contaminants are measured using the micron, a unit that represents one-millionth of a metre. To provide better context, here are some examples of micron-scale measurements that illustrate how small and impactful these particles can be within hydraulic systems.
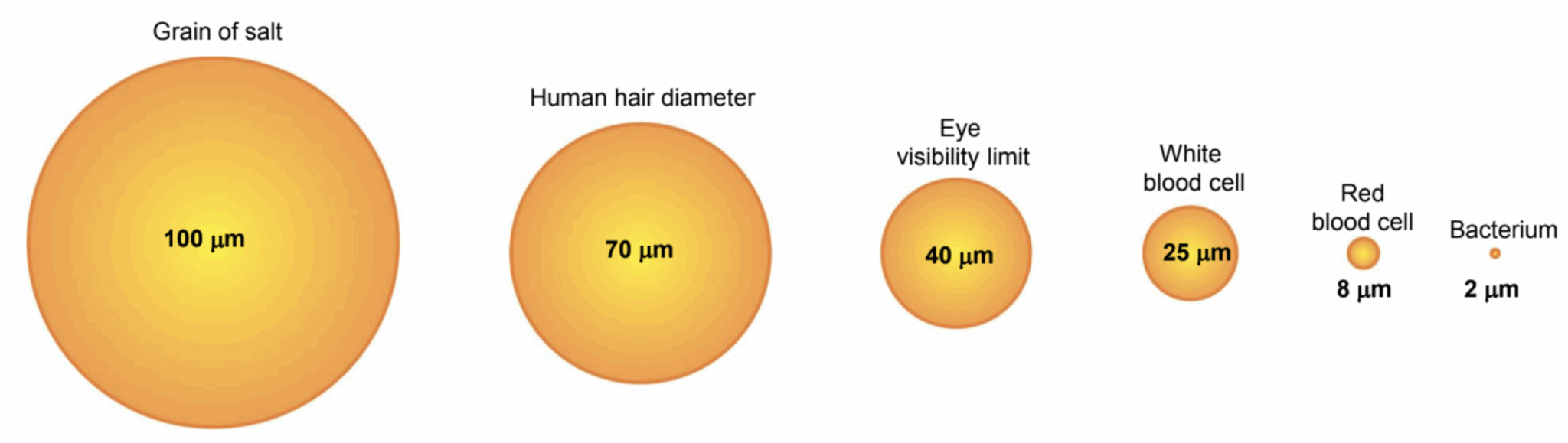
Impact of Contaminants on Hydraulic Systems
Contaminants can severely disrupt hydraulic system performance, leading to inefficiencies and premature wear.
- Energy Transmission: The presence of gas increases compressibility, while water lowers viscosity—both contributing to cavitation risks.
- Lubrication: Solid particles erode surfaces, compromising reflective finishes and overall system integrity. Unrelated fluids diminish lubrication effectiveness.
- Sealing Between Components: Abrasion and corrosion accelerate blow-by, degrading metal surfaces and elastomers.
- Fluid Properties: Foreign substances—whether liquid or gas—alter fluid quality, accelerating aging and diminishing essential performance characteristics.
Causes of Hydraulic System Failures
Studies conducted in Europe and the U.S. confirm that contamination is a primary contributor to hydraulic circuit malfunctions. The following breakdown illustrates the percentage impact of various failure causes:
- Temporal Decline: 15%
- Damaged Surfaces: 70%
- Corrosion: 20%
- Mechanical Attrition: 50%
- Abrasion
- Adherence
- Fatigue
- Incident-Related Faults: 15%
Mechanical attrition, the dominant factor within damaged surfaces, results from wear processes that compromise system integrity over time.
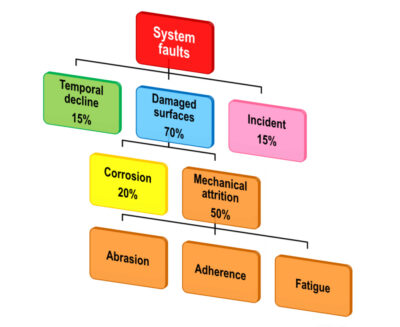
Understanding these failure modes allows for proactive maintenance and better contamination control, ultimately enhancing hydraulic system longevity and performance.
We are the first choice for customers in over 130 countries worldwide, supplying a vast selection of hydraulic brands and components. You are guaranteed impartial, technical advice and optimal solutions. Every time.
Discover more Free Educational Content from our Fluid Power Technical Knowledge Hub…
Hydraulic Fluid Contamination: Solids, Liquids and Gases
Hydraulic Fluid Contamination is responsible for the majority of system failures, making contamination control essential for optimal performance and longevity.
In this article, the first in collaboration with Ikron, we explored the three main types of hydraulic fluid contamination and their impact of system reliability.
Learn MoreThe Ultimate Hydraulic Oil Guide
Hydraulic oil is one of the most common fluids found in a hydraulic system and it is crucial that it is regularly checked and maintained. There are also many different types of available and it is important to choose the right oil for your system.
Learn MoreAn Introduction to Hydraulic Pressure and Flow
Understanding of the key principles of fluid dynamics is, essential for anyone who wishes to build or maintain hydraulic systems. One of the first concepts to understood is how the movement of fluids is quantified, namely flow.
Learn More