Even basic hydraulic systems usually have more than one possible flow path once the pump has drawn in fluid from the reservoir. The flow paths, or branches, are said to be in parallel with each other.
How to use pressure readings to diagnose problems in series and parallel hydraulic systems
Effective troubleshooting of problems in hydraulic systems requires a good understanding of flow and pressure readings.
We’ve introduced the concepts of pressure and flow in hydraulic systems in an earlier knowledge base article. In this article, we’re going to look at how pressure and flow can vary depending on the type of hydraulic system and what implications this has for hydraulic system troubleshooting.
Problems in a hydraulic system
As we know, a hydraulic system consists of at least five components, including the: selector valve, hydraulic lines, actuating units, reservoir, and pump.
These components can be configured in a variety of ways. And multiple components have the potential to create various competing flow paths. An understanding of these paths, including the flow paths that might result from a particular problem, is invaluable when trying to identify the cause of issues, such as a pressure drop, in a hydraulic system.
Unexpected flow paths are often at the root of hydraulic system problems. However, different system architectures will behave very differently in terms of fluid behaviour and flow paths. For this reason, it is important to understand the different types of hydraulic systems and the behaviour of fluid within them.
Different types of hydraulic system
A hydraulic system may have series connections or branches of parallel circuits – or both. These different system architectures will affect:
- how you calculate system and branch pressures,
- how you predict pressures and flow paths, and
- how you use pressure readings to troubleshoot different problems.
Understanding parallel and series systems
The characteristics of a parallel system are different to those of a series system. You will need to understand these differences to predict fluid behaviour.
For an overview of these concepts, we’re going to turn again to our friends over at LunchBox Sessions. Their fantastic online subscription content is served up in the form of bitesize lessons, videos and simulations.
Some taster sessions are accessible to all – and that’s where the images in this article have been sourced from… LunchBox Sessions have kindly allowed us to reproduce some of their e-learning content here. We encourage you to take a closer look at their site: it’s a fantastic online resource if you want to know more about how hydraulics and other industrial technologies work.
How parallel hydraulic systems work

In a parallel circuit, the hydraulic fluid will take the path of least resistance. Although it’s worth noting that it isn’t impossible for a parallel circuit to be shared by more than one parallel branch at the same time. Hydraulic systems can be multi-functioned through the specification of valves, pump size and hydraulic lines to adjust resistance and, therefore, system pressure.
Reading the system pressure of a parallel system helps you to understand which flow paths or branches are active. You can discover more about this in the following LunchBox Sessions video:
When overall system pressure changes unexpectedly, this can mean that a flow path has changed or is compromised.
How series hydraulic systems work
In a series circuit, the flow path runs from one component to another; a series of connections. This has implications for the flow and the system pressure. Each component can exert a restriction on the circuit, and each restriction (essentially a load) in series with the next, has a cumulative effect on the total pressure at the beginning of the branch.
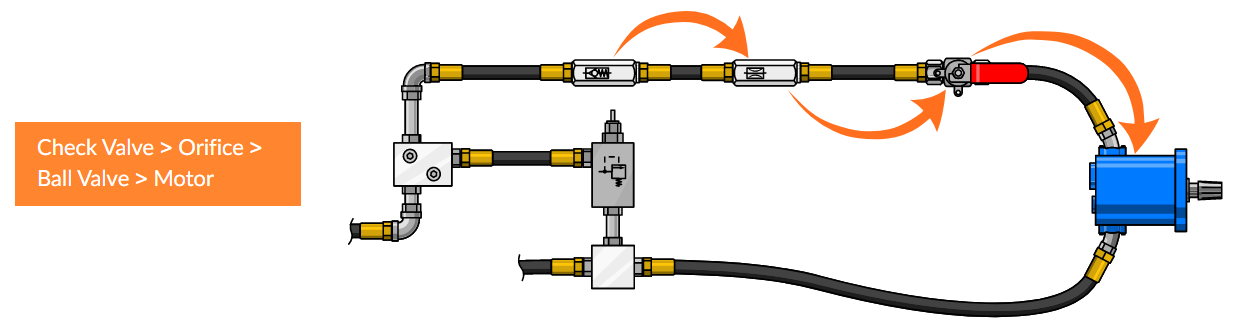
The overall system gauge will read the pressure of all downstream resistance – and this will affect how you calculate normal system pressure in series systems. In this next video, LunchBox Sessions provides a graphical explanation of this concept, based on a simplified series circuit that includes three spring-loaded check valves in a row:
These differences between how you calculate normal system pressure in series and parallel hydraulic systems clearly show why an understanding of how pressure operates in different types of systems will affect how you understand: a) when there is a problem and b) what might be causing it.
Using hydraulic system pressure to troubleshoot problems
For a visual example of how system pressure can be used to diagnose problems in a hydraulic system, we turn to another video provided by LunchBox Sessions. Using a similar simplified illustration of a hydraulic circuit featuring spring-loaded check valves, you can see how system pressure can be used to understand whether the expected flow path is active.
When system pressure deviates from what is expected, it is an indication that something is wrong.
- Low system pressure might indicate a leak or faulty component such as a valve not closing fully.
- High system pressure indicates greater resistance, which might come from a blocked flow path or a faulty component such as a clogged filter.
This is how understanding expected pressure helps you diagnose problems. For more information, take a look at LunchBox Sessions’ section on this topic.
If you are looking for support with hydraulic system design or troubleshooting, our technical team can help. Get in touch today!
Discover more of our collaborative content with Lunchbox Sessions…
Troubleshooting Hydraulic Systems: the Reservoir, Breather and Fluid Contaminants
The hydraulic reservoir plays an important part in hydraulic circuit design – storing hydraulic fluid when it isn’t being pushed through the hydraulic system.
While a “fluid storage tank” might seem like a very simple concept, the design and implementation of the reservoir is very important.
Learn moreAn Introduction to Hydraulic Pressure and Flow
An understanding of the key principles of fluid dynamics is, essential for anyone who wishes to build or maintain hydraulic systems.
One of the first concepts that must be understood is how physicists quantify the movement of fluids, namely flow.
Learn moreSpecifying Hydraulic Hoses
Hydraulic hoses convey the hydraulic fluid around the hydraulic system; they are not minor accessories.
No matter how big or small, a hose burst failure on a hydraulic system is always a catastrophic incident. Careful consideration must always be given to their specification and installation.
Learn more