Producing a quiet hydraulic system requires more than just quiet hydraulic components. Reducing noise to meet stringent sound-level specifications of today’s industrial hydraulic systems and machines takes careful engineering.
In order to design a quiet hydraulic system you firstly need to consider the hydraulic pump. In addition to producing sound directly, it also generates vibrations and fluid pulsations. These react with other machine parts which produce more sound.
Hydraulic pump selection
Hydraulic pumps generate more acoustic energy per unit of hydraulic power by running at high speed rather than at low. For this reason, a hydraulic pump should operate at 1200 rpm whenever sound is critical. Below 3000 PSI, the trade-off between pressure and hydraulic pump size for a given drive power has little effect on noise, so you are free to select any combination of these factors that otherwise meet your needs.
Mechanical isolation
To meet lower sound level limits, the hydraulic pump should be mechanically isolated from the rest of the machine or hydraulic system using anti-vibration mountings. All connections to the hydraulic pump must be made with flexible hose. Flexible hose will often reduce noise even where anti-vibration mountings are not used. It prevents vibrations from reaching other lines and hydraulic components to keep them from becoming sound sources.
In long lengths, this hose is, itself, a good sound generator so only short lengths should be used. For long runs, use solid pipes with short hoses at the ends. All long lines must be supported every metre or so, preferably with clamps providing vibration damping. Lines must not contact panels that are good sounding boards. Where they pass through such panels, allow sufficient clearance to prevent direct contact. Never use bulkhead fittings in such cases.
Acoustic isolation
The greatest sound level reductions are attained with the hydraulic pump acoustically, as well as mechanically, isolated. This requires that the hydraulic pump be completely enclosed in a non-porous shell weighing at least 10 kg per square metre of surface. No openings can be tolerated and all joints must be sealed with resilient gaskets or mouldings. Grommets of rubber or other soft material are used to close openings around piping and to prevent mechanical contact between the enclosure and piping.
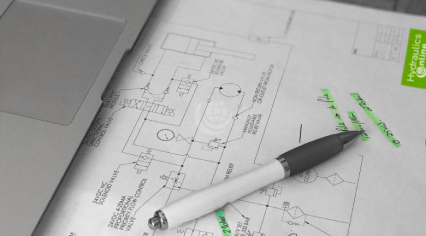
Fluids in a quiet hydraulic system
The condition of the hydraulic fluid being pumped is also important in the design of a quiet hydraulic system. Fluid viscosity, temperature and vacuum by themselves have no effect on sound levels. It is important to control them, however, to prevent the formation of entrained air or vapour bubbles that can double sound levels and reduce pump life.
A combination of high fluid temperature and inlet vacuum generates cavitation bubbles. However, at low temperatures, a high viscosity fluid in a very long suction line can also produce sufficient vacuum to cause cavitation.
Important methods of suppressing bubble formation include:
- Using short runs or large diameter inlet lines;
- Keeping the reservoir elevation close to or above that of the pump;
- Using low pressure-drop inlet filters that signal when they are producing high vacuums and need changing;
- Providing adequate fluid controls.
These are all good hydraulic practices that become increasingly important where you must achieve low sound levels.
Reservoirs
Reservoirs enable entrained bubbles to be released. These can come from sources other than the hydraulic pump inlet and are usually present in the fluid returning to the reservoir. Low reservoir temperatures reduce the rate of bubble escape and may result in incomplete release. As pointed out earlier, high temperatures promote bubble formation.
The best balance between these two alternatives is achieved by maintaining the temperature of oil leaving the reservoir in the range of 120-150 degrees F and the temperature of water-based fluids between 100-120 degrees F.
A simple reservoir has to be large to allow complete bubble release. By providing baffles to guide the fluid through a circuitous path and by locating return and pump inlet lines as far apart as possible, a reservoir holding between two to three minutes of maximum pump flow can be adequate.
Remember: if it's hydraulic, we can supply it, design it or repair it! How can we help?
Discover more free educational content from our Fluid Power Technical Knowledge Hub…
Using Pressure Readings to Diagnose Problems
Effective troubleshooting of problems in hydraulic systems requires a good understanding of flow and pressure readings.
In this article, we take a look at how pressure and flow can vary depending on the type of hydraulic system and the implications for hydraulic system troubleshooting.
Learn MoreAn Introduction to Hydraulic Pressure and Flow
Hydraulic systems are based on the principles of fluid dynamics; this important branch of science deals with the movement of fluids.
One of the first concepts that must be understood is how physicists quantify the movement of fluids, namely flow.
Lean MoreSpecifying Hydraulic Hoses
Hydraulic hoses convey the hydraulic fluid around the hydraulic system; they are not minor accessories.
No matter how big or small, a hose burst failure on a hydraulic system is always a catastrophic incident. Careful consideration must always be given to their specification and installation.
Learn More