Use this checklist when troubleshooting the most common hydraulic problems.
However, before diving into diagnostics, it’s essential to approach any hydraulic system with caution and clarity. Use this checklist as your starting point when troubleshooting the most common hydraulic problems—but first, make sure your senses (and safety protocols) are fully engaged.
Stay Safe Before You Start:
- Ensure all loads are fully lowered or mechanically secured before approaching the system.
- Never rely on a hydraulic control valve alone to hold a load in place.
- Isolate all power sources—both hydraulic and electrical—before beginning any inspection or repair.
- Fully exhaust any residual pressure locked within the system to prevent unexpected movement or fluid discharge.
Troubleshooting hydraulic problems requires more than just technical know-how—it demands a safety-first mindset. By taking these precautions, you protect both yourself and the integrity of the system.
Using Touch to Identify Common Hydraulic Problems
One of the simplest yet most effective diagnostic tools you have is your sense of touch. When troubleshooting common hydraulic problems, heat is often the first and most obvious warning sign.
If a component feels uncomfortably hot to the touch, it’s likely a sign of trouble. Excessive heat can indicate internal friction, fluid degradation, or a failing part. In particular, high fluid temperatures can:
- Reduce oil viscosity, weakening the protective film between moving parts
- Lead to inadequate lubrication, increasing wear and tear
- Cause long-term damage to pumps, valves, and seals
To prevent heat-related failures:
- Install a fluid temperature alarm to monitor system conditions in real time
- Regularly inspect components for abnormal heat levels
- Investigate and resolve any high-temperature readings immediately
Touch may seem basic, but it’s a powerful first step in identifying hydraulic system issues before they escalate into costly failures.
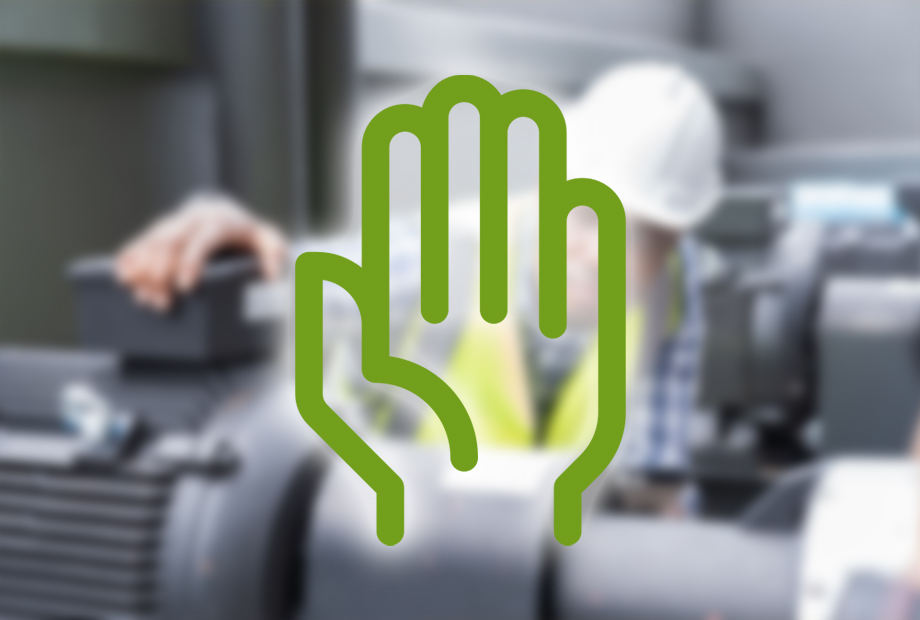
Look for Visual Clues of Common Hydraulic Problems
When troubleshooting common hydraulic problems, your eyes can often detect early warning signs before a failure occurs. One of the most noticeable indicators is a drop in system performance—such as longer cycle times or sluggish actuator movement.
In hydraulic systems, flow directly controls actuator speed and responsiveness. So if you notice a loss of speed, it typically points to a loss of flow. Keep an eye out for:
- Slow or delayed actuator response – often caused by restricted flow or pump inefficiency
- Erratic or inconsistent actuator movement – a strong sign of air trapped in the system
- Visible leaks or fluid misting – indicating seal failure or hose damage
- Foaming or discoloured fluid – suggesting contamination or aeration
Entrapped air is a particularly common culprit behind inconsistent motion. It compresses under pressure, causing spongy or unpredictable actuator behaviour.
Want to learn more? Check out our full article on Air contamination in hydraulic systems for deeper insights and prevention tips.
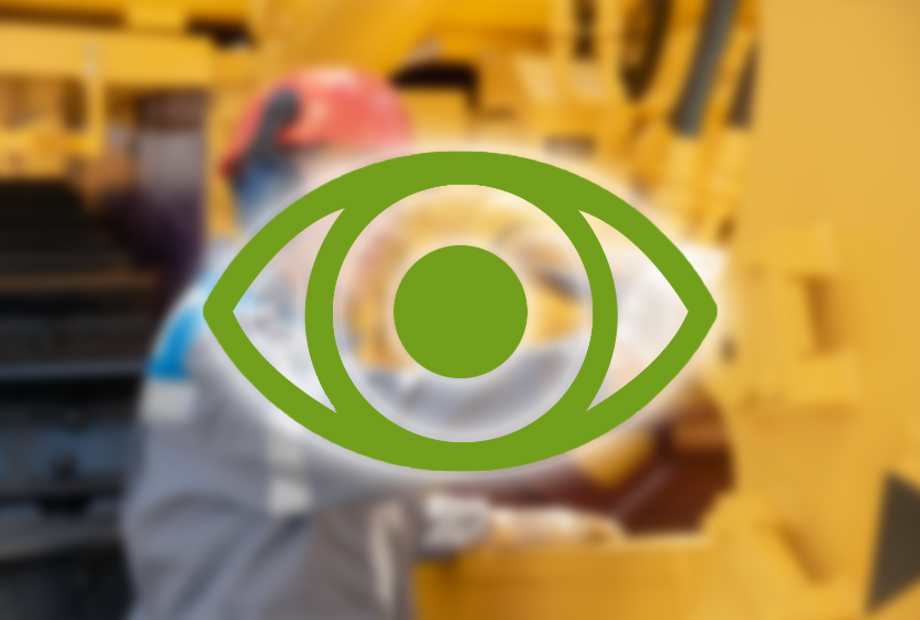
Listen for Sounds That Signal Common Hydraulic Problems
Sound is a powerful diagnostic tool when troubleshooting common hydraulic problems. Unusual noises—such as banging, knocking, or whining—often point to serious internal issues like aeration or cavitation.
These two conditions may sound similar, but they have very different causes and consequences:
- Aeration occurs when air enters the hydraulic fluid, often through loose pump inlet fittings or damaged intake lines.
- Cavitation happens when vapour bubbles form and collapse within the fluid due to low pressure, causing shockwaves that erode metal surfaces.
Cavitation is especially destructive. It can lead to:
- Metal erosion inside pumps and valves
- Fluid contamination from dislodged particles
- Premature failure of critical hydraulic components
To prevent these issues:
- Inspect and maintain pump intake lines regularly
- Ensure all clamps and fittings are tight and leak-free
- Monitor for changes in noise levels, especially during startup or under load
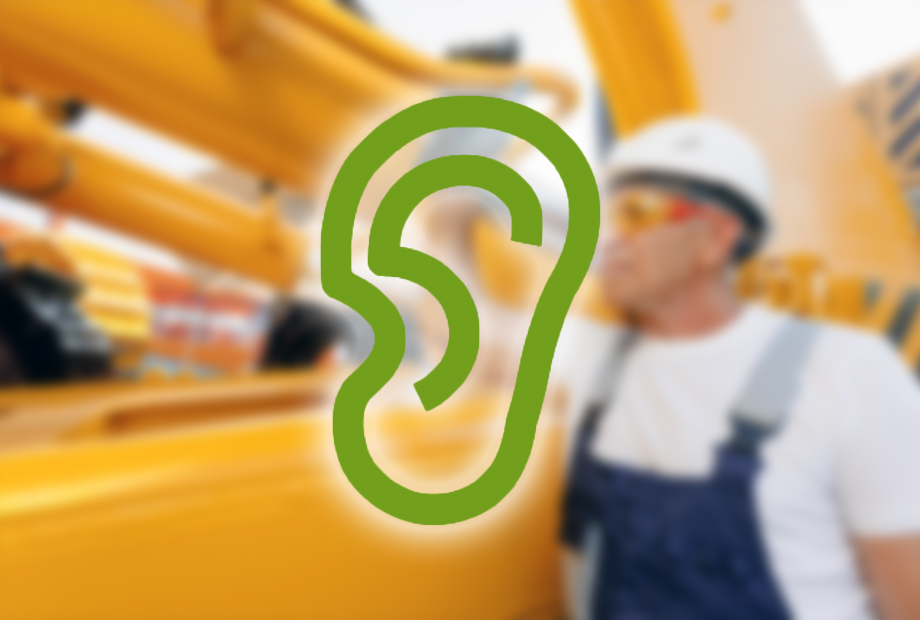
Proactively listening for abnormal sounds—alongside tracking fluid temperature and cycle times—can help you catch problems early, reduce downtime, and extend the life of your hydraulic equipment.
A Scent-Based Signal of Common Hydraulic Problems
Your sense of smell can be surprisingly useful when diagnosing common hydraulic problems—especially when it comes to detecting overheating. One of the most telling signs of thermal stress in a hydraulic system is the smell of the oil itself.
If the hydraulic fluid emits a harsh, bitter, or burnt odor, it’s a strong indicator that the oil has been exposed to excessive heat. This usually means the oil’s additive package—responsible for lubrication, anti-wear protection, and oxidation resistance—has broken down.
What to do if your hydraulic oil smells burnt:
- Replace the oil immediately to prevent further damage to pumps, valves, and seals
- Inspect for root causes of overheating, such as restricted flow, excessive pressure, or poor ventilation
- Monitor fluid temperature regularly to catch heat-related issues early
To prevent overheating in the first place, focus on two key strategies:
- Reduce hydraulic oil temperature – by improving system efficiency or reducing load
- Increase heat dissipation – through better cooling systems or heat exchangers
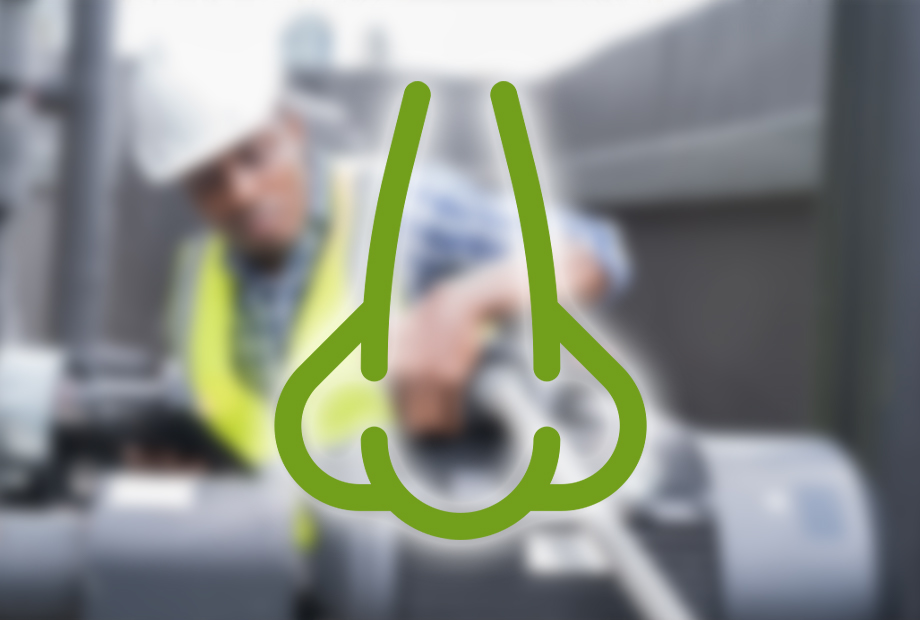
We’re a hydraulics ‘hub’, offering thousands of possibilities… how can we help?
Discover more Free Educational Content from our Fluid Power Technical Knowledge Hub…
Troubleshoot Air Contamination in a Hydraulic System
A contaminant is defined as anything that impairs the performance of the hydraulic system and its components. Air contamination in a hydraulic system can be found in hydraulic fluid in four different forms…
Learn MoreSpecifying Hydraulic Hoses
Hydraulic hoses convey the hydraulic fluid around the hydraulic system; they are not minor accessories. Careful consideration must always be given to their specification and installation.
No matter how big or small, a hose burst failure on a hydraulic system is always a catastrophic incident.
Learn MoreThe Vital Role of Hydraulic Cylinder Seals
Hydraulic cylinder seals are commonly found in applications where components are exposed to liquids. They play a vital role within the hydraulic system, as they enable the transfer of liquid power into linear motion.
Learn More