The hydraulic fluid is one of the most important components in the system yet it is often overlooked…
The fluid is the medium for the transmission of power and without sufficient fluid, no work can take place. It also performs functions such as lubrication, heat transfer and allows the conveyance of debris and contamination.
How hydraulic fluids affect pump performance
Hydraulic components and the hydraulic fluid work together to run the hydraulic system. The critical role of hydraulic fluid, appropriate fluid type, viscosity, and quality are all essential requirements for fluid selection. If the wrong fluid is selected the system will operate at a substandard rate with this leading to catastrophic failures of components such as decreased system efficiency, lack of lubrication, reduced fluid and component life, corrosion, erosion, sludge and varnish formation, and excessive heat generation.
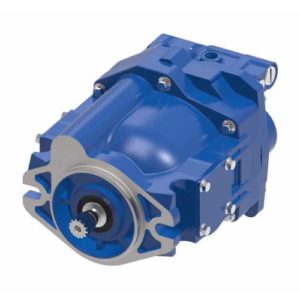
In addition to fluid properties and quality, contamination also affects system performance significantly. Contamination can generally originate from four sources: contaminated oil, built-in contamination, ingressed contamination, and internally-generated contamination. It can lead to decreased efficiency, component wear, and other adverse impacts. Studies indicate that more than 70 percent of hydraulic system failures are due to contamination and can reduce hydraulic efficiency as much as 20 percent before a system malfunction is recognised.
Fluid properties to consider
There are various different properties which can affect a fluid’s performance. Viscosity is arguably the most important. Viscosity describes a fluid’s resistance to flow. Viscosity accounts for volumetric and mechanical efficiency, heat generation, lubrication of components and other properties such as heat dissipation, filterability and air release.
Low viscosity can cause damage to system components as improper lubrication causes metal-to-metal contact within components leading to wear and potential contamination. Low viscosity also reduces volumetric efficiency of pumps and motors through increased internal leakages.
On the other hand, high viscosity causes decreased mechanical efficiency due to the increase in resistance to flow. The increased resistance to flow will also cause an increase in excess heat, elevating fluid temperatures. High viscosity can lead to cavitation and erosion caused by a collapsing air bubble or vacuum bubble. In addition, lubricants may not reach areas with tight clearances, causing failures due to inadequate lubrication.
Viscosity itself is affected by temperature. Suitable viscosity grade fluid needs to be selected for each application based on the operating temperatures. The fluid viscosity at operating temperature must meet the viscosity recommendations of the system components, primarily the pump. Minimum, normal, and maximum operating temperatures need to be considered for selecting the fluid viscosity grade.
Overall efficiencies of hydraulic components are related to mechanical efficiency and volumetric efficiency. Mechanical efficiency is related to frictional losses and drag due to fluid viscosity, and volumetric efficiency relates to internal leakages. Both volumetric and mechanical efficiencies depend on the viscosity of the fluid. The particular range of viscosity at which overall efficiency is maximum is typically selected as the optimum range for the specific components. Viscosity recommendations should be considered for all system components, but viscosity recommendations for pumps and motors should be given prime importance.
Anti-wear (AW) properties of fluids are another crucial parameter to be considered. Good AW properties are required to maximise hydraulics system performance and component life. The fluid must be properly formulated and have adequate AW additives. The AW additives form a thin layer on the mating surfaces and help prevent metal-to-metal contact at boundary lubrication conditions.
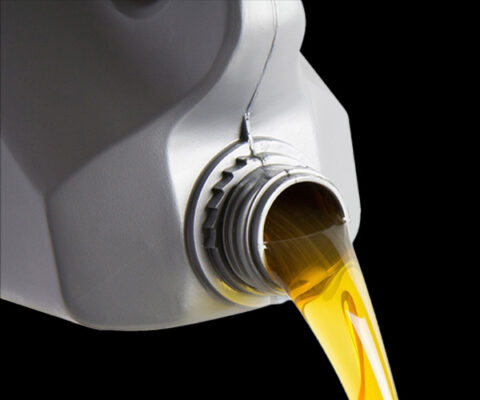
Insufficient AW properties can lead to cold welding and scuffing in the boundary lubrication regime, resulting in removal of surface material. Anti-wear properties are essential for both rolling and sliding contact, but the requirement for sliding contacts is more critical, as stick-and-slip type movement can occur.
Even the best machined surfaces have asperities (hills and valleys). When the asperities come in contact at heavy load, they can become joined by cold welding. If the applied force is large enough to break the welding, the object suddenly moves. This causes material removal from surfaces. High additive reserve is recommended for severe applications, to allow the surfaces to slide or roll over each other without any surface damage.
Other properties to consider include:
1. Viscosity Index (VI)
An empirical, unit-less number indicating the effect of temperature change on the kinematic viscosity of an oil. Liquids become less viscous when heated. A high VI indicates a relatively small change of viscosity with temperature. High VI (multi-grade) fluids are recommended for applications at wide operating temperatures or at extreme environmental conditions. In general, high VI fluids are recommended for mobile applications, as they are exposed to environmental changes and high operating temperatures. You can read more in our article: The lowdown on hydraulic oil viscosity.
2. Shear Stability
This is the measure of a fluid’s resistance to shearing. Polymers, known as VI improvers, are used to make high VI fluids with low shear stability will quickly break down, resulting in thinning of oil. Viscosity after shear also needs to be considered for applications with VI-improved fluids.
3. Thermal and Oxidative Stability
Oxidation is the chemical reaction of oxygen with oil, generating acidic by-products. The rate of oxidation is accelerated by high temperatures, water, acids generated due to oxidation, and presence of metal catalysts such as copper. The rule of thumb is: oxidation doubles with increase of temperature by every 10°C. Oxidation will lead to increased viscosity, total acid number (TAN), generation of varnish and sludge, and darkening of fluid. The rate of oxidation can be reduced by reducing fluid temperature and using fluids formulated with quality base stocks, anti-oxidant additives, and thermally stable AW additives.
4. Hydrolytic Stability
Hydrolysis is the chemical degradation of lubricants by reaction with water. Lubricant additives, especially zinc-based additives, will react with water, forming acidic by-products. The presence of metals such as copper can act as a catalyst. Ester-type base stocks also hydrolyse in the presence of water. Lubricants with good hydrolytic stability will resist hydrolysis.
5. Filterability
Fine filters used in hydraulic systems may exhibit premature filter plugging due to inappropriate formulations, water contamination, and fluid degradation. Measurement of filterability helps predict fluid behaviour in filtration applications, before use in a system.
6. Demulsibility
The ability to release water from a water-oil mixture. This characteristic is important for the equipment operating in humid climates, where the possibility of water contamination is high
7. Rust and Corrosion Inhibition
Hydraulic fluids are generally formulated with rust and corrosion inhibitors. The rust inhibitors get deposited as thin film on the metal surfaces and enable protection from rust. The corrosion additives hinder hydrolysis and prevent formation of acidic materials which causes corrosion. The ability of a fluid to prevent rust and corrosion can be measured by a rusting test using distilled water, saltwater, and a steel specimen.
8. Material Compatibility
Different rubber and elastomer components, including hoses, accumulator bladders, seals, and gaskets, are used in hydraulic systems and have different compositions, or recipes. Because of these varying compositions, fluids are tested for their compatibility with most commonly used elastomers to predict the life and performance with that particular fluid.
9. Air Release
Suspended entrained air can cause many abnormalities such as poor system efficiency, system failure through erosion (similar to cavitation), and fluid degradation through micro-dieseling. Micro-dieseling occurs when air bubbles move from a low- or negative-pressure area to a high-pressure area, get heated up due to compression, and carbonize oil at the bubble interface, resulting in carbon by-products and oxidation. Air release characteristics have more significance in systems with relatively short residue time. An air-release test can identify the ability of a lubricant to separate entrained air.
10. Foaming Tendency
Foaming is a common problem for hydraulic systems. Large volumes of foam can cause overflow of reservoirs. Factors that lead to foaming are contamination, degraded fluid, air entrainment, and poor system design. Hydraulic fluid formulations contain foam inhibitors, but very higher dosages can give adverse effects. Foaming tendency test describes the volume of foam generated immediately after the fluid is agitated and aerated. Foam stability measures the volume of foam remaining after a specific time from the stoppage of aeration.
11. Volatility
Volatility is the tendency of a fluid to vaporise rapidly. While generally not as critical for hydraulic fluids as for motor oils due to limited or no exposure to high temperatures and lower operating temperatures of hydraulic fluids, volatility is still a parameter to consider. Mineral base oils are mixtures of hydrocarbons of different size. At high operating temperatures, smaller molecules may escape from the oil, decreasing oil volume and increasing fluid viscosity. Improper base oil selection and blending can lead to higher volatility.
The impacts of using the wrong fluid
What happens if an improperly matched fluid is used in a pump? The answer can vary, depending on the degree of mismatch. As noted earlier, fully formulated fluids should have balanced properties. Excessive variation in any given parameter can cause direct or indirect impacts. For example, a fluid incompatible with certain rubber materials may cause failure of gaskets and other components. A single issue can cause catastrophic failure: poorly maintained systems may fail catastrophically due to one or more reasons. Contamination, along with incompatible fluids, can lead to component failures.
Summary
When selecting the correct hydraulic fluid, you should consider all factors regarding the system, the operating conditions and the application involved. Hydraulic failures can be catastrophic to components and applications. Always consider the effects of a breakdown when designing an application and selecting a hydraulic fluid; the fluid must be suitable for all system components and suitable for the operating environment. This is the key to a long-lasting healthy system.
Reproduced with kind permission from Eaton Hydraulics.
Authorised and regulated by Eaton. All rights reserved.
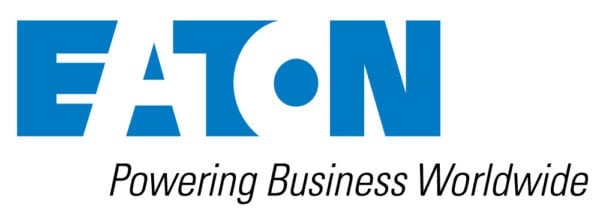
Hydraulics Online is the first choice for customers in over 130 countries worldwide, supplying a vast selection of hydraulic brands and components. You are guaranteed impartial, technical advice and optimal solutions. Every time.
Expand your Hydraulics Knowledge and explore more from our Fluid Power Technical Knowledge Hub…
Using Pressure Readings to Diagnose Problems
Effective troubleshooting of problems in hydraulic systems requires a good understanding of flow and pressure readings.
In this article, we look at how pressure and flow can vary depending on the type of hydraulic system and what implications this has for hydraulic system troubleshooting.
Learn MoreTroubleshooting Hydraulic Systems: the Hydraulic Reservoir, Breather and Fluid Contaminants
The hydraulic reservoir plays an important part in hydraulic circuit design. It stores the hydraulic fluid when it isn’t being pushed through the hydraulic system.
However, there are some design considerations when specifying a this vital component!
Four Reasons to Switch to a Smarter Hydraulic Pump Drive System
From efficiency, controllability and versatility to noise and vibration control, learn how smarter hydraulic pump drive systems can benefit industrial applications.
Learn More