Check valves are unseen and undervalued. These valves are found in just about every mobile and industrial hydraulic system on the planet. Simply put, if there’s a pump, most likely you will find a check valve.
Check valves keep the fluids flowing in the desired direction to prevent damaging flow or pressure in the reverse direction. They can also be used in applications to maintain a system pressure for optimum system readiness and performance. Surprisingly, for a valve that performs such a critical function, a check valve incorporates very few components – the body, poppet, spring and retainer.
Give this essential valve its due
Considering its wide use, engineers, maintenance technicians and even end users should have a basic understanding of the function that this essential component serves in their systems. More often, however, that’s not the case.
Generally, misunderstood in their function and importance, when you mention check valves, the responses range from “they just don’t work” to “never use them.” As stated earlier, a check valve exists to keep fluid flowing forward while helping to prevent reverse flow of fluids within a system. That makes them important for many reasons.
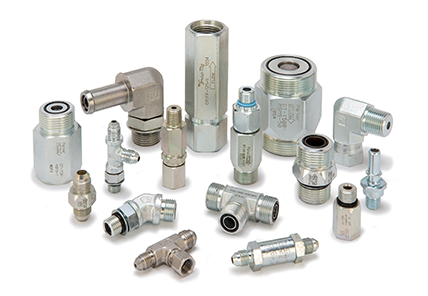
Where and why to use a check valve
- Pump protection: Systems with multiple pumps will experience extended service life when check valves are utilized to isolate and protect these components from system failure. Examples of this could be a high/low pump or even an emergency pump on a mobile system.
- Cooler protection: Damaging pressure spikes can be avoided by diverting pressure/flow. Examples are widespread in mobile and industrial applications with hydraulic and lubrication oil coolers.
- Actuator flow control: Whenever speed control of an actuator is needed for operator safety, use a check valve in the lift and lower circuit. Examples are forklifts, aerial work platforms or hood systems on large equipment.
- Keeping prime / pressure: Commonly used on fuel systems to maintain prime, for ease of maintenance and for quick start up. Also, check valves are essential for use on hydraulic systems to prevent pump oil starvation at start up.
The most innovative check valves on the market
Like any product, quality makes the difference. When that product is a check valve, you want the best on the market. There’s just too much at stake to consider anything else. That’s where Parker comes in. Parker’s check valves are engineered to perform under the most demanding circumstances. Offered in many configurations, their in-line style check valves are available in a variety of sizes, pressure ratings, flow capacities and crack pressures to satisfy most hydraulic system applications.
Parker DT Series check valves cover the widest variety of applications. These hard seat check valves are offered in sizes from ¼” to 1-1/2” with the added benefit and convenience of compact design. Select sizes are also available in 45°, 90° and tee shape fittings which can help optimize system design by reducing labor and leak points. If you are unsure where to start looking for check valves, the DT Series is a great first option.
Their CV Series check valves are another hard seat check valve option for your application. Built using a rugged modular design that results in less pressure drop for increased performance in critical applications.
The CPIFF Series check valves are a soft seat check valve option for your application. Soft seats are often used in applications where zero backflow is allowed.
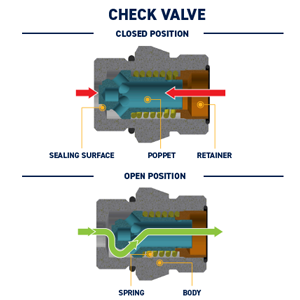
One of the most important valves for any system
Finally, a check valve is a relatively inexpensive component that protects significantly more expensive system components. A company can save thousands of dollars or pounds by implementing check valves and protecting these vital components. With so much on the line, it only makes sense to choose a reliable and high-quality product that can deliver under the most extreme conditions – as you can expect from Parker.
This article was contributed by Matt Walley, product sales manager, Quick Coupling Division, Parker Hannifin. Licensing for the images came with permission from the Parker Hannifin Media Manager collection.
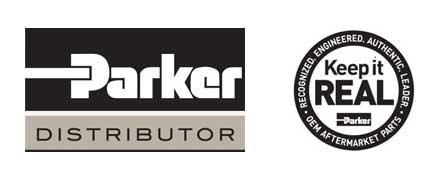
We are official suppliers for Parker hydraulic equipment and components and trusted by customers in 130 countries worldwide! How can we help?
Discover more free content from Parker in our Fluid Power Technical Knowledge Hub…
Advantages of Helical Hydraulic Actuators in Heavy-Duty Applications
Hydraulic actuators cause engineered equipment to move, slide, rotate and lift by converting energy from pressurised fluid and hydraulic power units. Depending on the type of machinery involved and the desired movement needed, there are a variety of linear and rotary actuators available to best match the needs of the designer.
Learn MoreThe Parker V16 Variable Displacement Motor
Parker V16 Series is the next generation of variable displacement, bent-axis motors. It further develops Parker’s well-known V12 and V14 hydraulic motor series. Here’s three reasons to choose this efficient hydraulic motor for your mobile application
Learn More10 FAQs you should know about Power Take-Offs
A Power Take-Off, or PTO, gives a truck versatility beyond its usual function of providing transportation for materials. It directs power to the auxiliary equipment to allow it to perform work at the site or en route.
Learn More