Hydraulic system contamination is responsible for 80% of system failures – whether through the introduction of contaminated fluid or more progressively through, for example, metal surface wear, corrosion or cavitation.
Hydraulic system contamination can be caused by either the presence of solids, other liquids or gases in the hydraulic fluid. In this article, produced in conjunction with MP Filtri, we look at the effects of each, best practice for prevention and how best to remove contaminants already in your system.
Liquid Contamination
This can include the presence of water due to condensation or external infiltration or acids. Water is a chemical contaminant in oils; at 100% relative humidity water forms as bubbles in hydraulic systems. The effects can be dangerous if water is present and is not monitored and controlled properly.
How water affects your system
When free water exists in an oil, the bubbles it forms can interfere with particle counts and affect system performance and outputs. Excess water will typically also give a ‘dirtier’ reading than the actual system cleanliness – oil may turn cloudy or opaque which may mean that the oil should be replaced. To extend systems life, oil should therefore always remain relatively translucent.
Poor water monitoring and control can lead to: shorter component life; wire erosion and vaporous cavitation; hydrogen embrittlement; oxidation and component wear. All of these can exist depending on individual system designs and have the potential to lead to catastrophic failure.
MP Filtri recommend that you set a maximum alarm setting for water content in your oil, and where possible aim to operate well within this limit so that water never becomes a problem. Their water sensor options can monitor levels of water in your hydraulic oil allowing you to keep your system in good condition.
Removing the risk of water-induced failures
To remove the risk of water induced failures, hydraulic system contamination management and operator training should cover:
- Oil management and handling
- Using breathers or tank headspace protection
- Washing down of systems and protection during this operation
- System equipment IP ratings and susceptibility to moisture ingress
- Formation of condensate on the surrounding area
- Secondary sealing for critical applications
- Storage of oil drums
- Periodic draining of particularly susceptible systems
How can I prevent water from getting into the system?
Hydraulic fluids should always be kept in sealed containers stored in relatively dry environments until needed. Lids should be checked routinely and tightly secured. Moisture from rainfall or humidity, can cause water ingress into the container. As some fluids are hygroscopic, meaning they absorb moisture, always use lids on tanks and, if necessary, use a hygroscopic breather to further reduce the risk of moisture entering your system.
Gaseous Hydraulic System Contamination
Gaseous hydraulic system contamination can be caused by air entering the system perhaps through an inadequate oil level in the tank, drainage in suction ducts, or incorrect sizing of tubes or tanks. You can evaluate how much air is in your system by measuring the reservoir level pressurized and then un-pressurized. If the fluid level in the tank is lower when pressurised, this could indicate that air is present in the system – some maintenance may be required.
Aerated fluid can cause a variety of problems with differing implications for performance, maintenance costs and safety. These include:
- Increased fluid temperatures
- Reduced lubricity
- Cavitation and system component erosion
- Noise
- Dampening and poor system control
How can I limit the amount of air getting into my system?
When measuring particulate contaminants, steps should be taken to ensure that the product is not exposed to aerated fluid. The following factors should be considered to avoid aerated fluid in new and existing installations:
- Significant or sudden pressure drop
- Hydraulic shock resulting from sudden operation of valves and pumps
- Inadequate operating conditions for different types of pump
- Inadequate diffusion of the fluid at the return tank
Extra care should also be taken when replacing system components. Where necessary and/or possible, components should be pre-filled with new, filtered oil before installation. This will reduce the amount of air being placed into the system.
How can I remove air already in my system?
There are a number of ways to remove air from a system, but the following are probably the most simple and commonly used:
- Reservoir air bleed valves
- Baffled Reservoir tanks
- System maintenance procedures
- Adequate diffusion back to tank
- Reservoir level
Reservoir bleed valves are good, but, as their name suggests, their use is limited to the reservoir only. They may not detect air in other parts of the system. It is certainly good practice to use these devices on closed systems.
Solid Contaminants
Solid contamination can be caused by many factors including: rust, metal particles, slag, fibres, silica, dirt or dust, rubber particles, paint particles, silt, bacteria or additives. Examining the type of contaminant may help to identify where and how it is entering the system. Understanding this may then enabling preventative actions to be taken.
Good work practices are essential to avoid this type of hydraulic system contamination and include the following:
- No food and drink nearby
- Pre-filter your oil before placing into or returning back to the tank
- Use a dedicated funnel for a particular type of fluid when pouring into the tank
- Have a dedicated fill point for the reservoir
- Use a sloped or conical tank design with an outlet at the bottom, so that contaminants are captured by the first bank of filters
- After filling or topping up with new oil, let the system flow and filter, reaching a natural equilibrium point before using live in your process
What effect does solid contamination have on my system?
Contamination can result in mechanical wear and place excessive stress on system components, such as pumps and valves. It can also cause corrosion, lead to a loss of protective coatings on components and clog orifices, nozzles, and jets. Operating temperatures can increase and fluid compressibility can change.
One of the main areas of degradation is the formation of oxygenated & heavy polymeric compounds. These compounds are often in-soluble and settle out of the fluid as a gel or sludge. These compounds form more quickly in the presence of water and metal – care should be taken to remove these types of contaminant from your oil.
When a fluid is contaminated its viscosity will normally increase, leading to higher than normal friction and subsequent temperature increases. This can reduce system efficiency, wear components and affect compression rates. Contamination can also lead to catastrophic failure.
What factors can affect particle distribution and concentration with my system?
A hydraulic systems’ construction is mainly metal or elastomer/textile-based. Over time, and in reaction to changing fluid conditions such as temperature, pressure and chemical decomposition, these materials can become susceptible to corrosion and leach out contaminants into the system.
As a system operates, contamination is generated and needs to be controlled. It is physically impossible to achieve 100% efficiency in any given system; some particles will always get through filtration. It is generally assumed that the fluid is “clean” downstream of any filtering and purification, although this may not be the case.
Homogeneity is important in accurately assessing system contamination: a homogenous solution is uniform in its composition and particles are evenly distributed within it. The majority of real world systems are heterogeneous (un-evenly composed) and when taking measurements this must be considered as a significant variable between tests.
Viscosity, temperature, electrical conductivity, surface tension are some of the factors that can adversely affect the overall quality of your fluid.
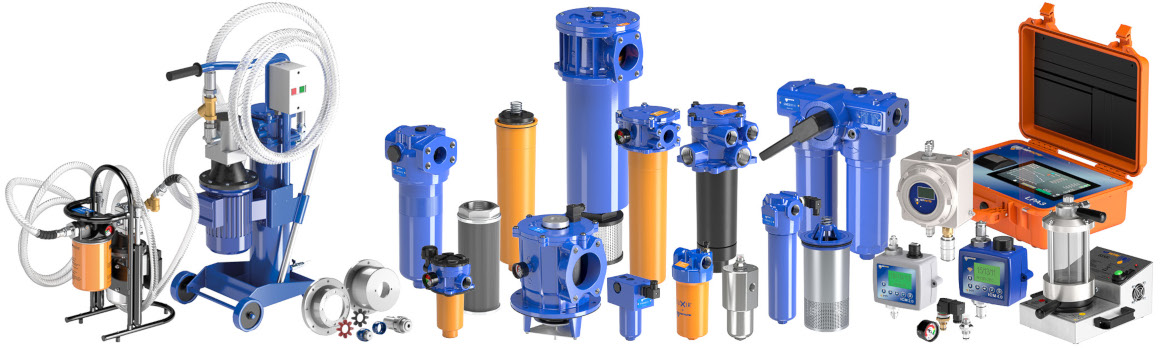
Hydraulics Online are the first choice for customers in over 130 countries worldwide, supplying a vast selection of hydraulic brands and components. You are guaranteed impartial, technical advice and optimal solutions. Every time.
Expand your hydraulics knowledge with more from our Fluid Power Technical Knowledge Hub…
Using Pressure Readings to Diagnose Problems
Effective troubleshooting of problems in hydraulic systems requires a good understanding of flow and pressure readings.
In this article, we look at how pressure and flow can vary depending on the type of hydraulic system and what implications this has for hydraulic system troubleshooting.
Learn MoreTroubleshooting Hydraulic Systems: the Hydraulic Reservoir, Breather and Fluid Contaminants
The hydraulic reservoir plays an important part in hydraulic circuit design. It stores the hydraulic fluid when it isn’t being pushed through the hydraulic system.
However, there are some design considerations when specifying a this vital component!
Learn MoreMP Filtri LPA3 – a state-of-the-art Portable Particle Counter
MP Filtri’s next-generation LPA3 portable particle counter followed after an exhaustive three-year research and development programme. It delivers a market-leading feature set including outstanding speed and accuracy and is fully portable. In a nutshell this enables operators to enjoy the functionality of the lab even when out in the field!
Learn More