Routine maintenance is key to sustaining a healthy hydraulic system – reducing downtime, extending component lifespan, and cutting operating costs.
While we’re always here to help if things go wrong, we’d rather help you get things right from the start. By following these six straightforward steps, you’ll protect system performance and make a smart investment of time and money.
Step 1: Maintain Optimal Fluid Temperature and Viscosity
A healthy hydraulic system starts with selecting the right fluid—and keeping it within safe operating limits. The temperature and viscosity of hydraulic oil directly impact component lubrication, system responsiveness, and energy efficiency.
Key considerations:
- Know the minimum and maximum operating temperatures for both your system and ambient environment;
- Choose a fluid with the correct viscosity grade and performance additives suited to those conditions;
- Regularly monitor fluid characteristics to detect early signs of breakdown, thickening, or thermal stress.
Maintaining proper fluid temperature and viscosity helps ensure consistent lubrication, reduces wear, and protects seals – especially in high-pressure circuits or extreme climates.
Need help selecting the right oil? Check out our Hydraulic Oil Guide for expert recommendations.
Step 2: Keep Hydraulic Fluid Clean
Clean fluid is essential for a healthy hydraulic system. Contaminants – like particles and air – can quietly sabotage performance, cause component wear, and lead to sudden failure.
Why Contamination Matters
- Solid particles can scratch, jam, or erode valves, pumps, and actuators;
- Air contamination (yes, air counts too!) introduces sponginess, heat build-up, and cavitation;
- Abrasive wear from dirty fluid leads to shortened component life and increased maintenance costs.
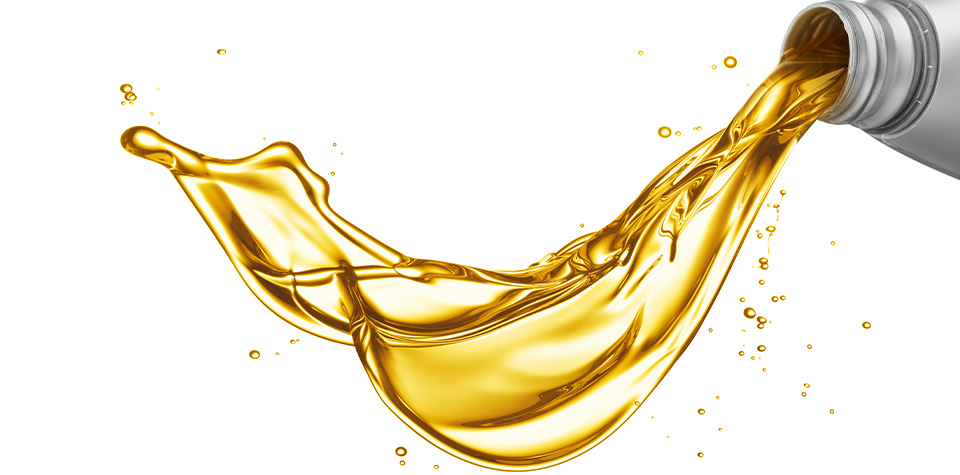
How to Keep Fluid Clean
- Choose the right hydraulic filter based on fluid type, pressure range, and expected contaminant load;
- Monitor filter condition and replace at intervals, not simply after clog indicators trigger;
- Prevent air ingress during maintenance and operation – tight seals and proper filling procedures matter.
Clean fluid is the lifeblood of reliable performance. Prioritising contamination control helps you avoid unplanned downtime and ensures your hydraulic system stays responsive and efficient.
Step 3: Maintain Manufacturer’s System Settings
A healthy hydraulic system depends on precise and consistent operation – so keeping system parameters in line with manufacturer specifications is non-negotiable.
Why it matters
- Correct settings ensure optimal pressure, flow rates, and actuation speed
- Deviations can cause premature wear, overheating, or erratic system response
- Matching original specifications simplifies diagnostics and future upgrades
What you should do
- Integrate system setting checks into your routine maintenance schedule
- Verify adjustments after component replacements or fluid changes
- Refer to OEM documentation for calibration guidelines, tolerances, and adjustment procedures
Building this into your standard maintenance workflow helps avoid costly resets and safeguards system longevity.
Step 4: Follow Proper Hydraulic System Commissioning Procedures
Commissioning is a critical step in establishing a healthy hydraulic system – and rushing through it can lead to component damage that can be invisible until performance suffers down the line.
Why commissioning matters
- Start-up is when seals seat, valves cycle, and fluid begins circulating under pressure – mistakes here can quietly shorten service life;
- Initial damage may not be obvious but can cause long-term wear, leakage, or erratic system behaviour.
Best practices
- Follow the manufacturer’s step-by-step commissioning process, including flushing, venting, and pressure ramping;
- Verify component alignment, fluid levels, and filter placement before powering up;
- Document system parameters and baseline performance for future diagnostics.
Treating commissioning as a precision process – not a box to tick – sets your hydraulic system up for smooth, reliable operation.
Step 5: Replace Hydraulic Components Proactively to Prevent System Failures
Preventive replacement is essential for sustaining a healthy hydraulic system. Waiting for a component to fail can create a ripple effect – damaging adjacent parts, introducing contamination, and increasing downtime exponentially.
Why proactive replacement matters
- Sudden failures often lead to secondary damage, especially in high-pressure circuits;
- Emergency repairs cost more and disrupt operations far longer than scheduled replacements;
- Worn components may still function – but degrade system performance, efficiency, and safety.
Best practices
- Use manufacturer lifespan guidelines and operating history to schedule proactive replacements
- Track usage hours, pressure cycles, and temperature data to anticipate wear rates
- Inspect seals, hoses, and valves regularly for early signs of fatigue or abrasion
Being proactive with part replacement isn’t just about avoiding breakdown – it’s a smart investment in long-term reliability and cost control.
Step 6: Learn From Failures to Strengthen Your Hydraulic System’s Health
Even in a healthy hydraulic system, things can occasionally go wrong. What matters most is how you respond – turning mistakes into valuable insights that lead to smarter procedures and long-term reliability.
Post-failure protocol
- Conduct a full failure analysis to understand root causes and pinpoint procedural weaknesses;
- Document your findings and update maintenance routines, commissioning steps, or component selection accordingly;
- Avoid repeating mistakes by changing habits, not just parts.
Mistakes are inevitable – but repeating them doesn’t have to be. A solid post-failure strategy sets your team up to prevent future breakdowns and build a more resilient hydraulic system.
Got a Repair Challenge?
If you’re facing a repair challenge, our expert team is here to help. We offer a free assessment that includes:
- Full unit teardown and diagnostic evaluation;
- Detailed repair recommendations with itemised quotes;
- Breakdown of which components can be salvaged or re-used before any work begins.
We’re your go-to hydraulics hub – thousands of possibilities, one trusted team. How can we support you today?
Discover more Free Educational Content from our Fluid Power Technical Knowledge Hub…
Troubleshooting Hydraulic Systems: the Reservoir, Breather and Fluid Contaminants
The hydraulic reservoir is far more than a fluid storage tank – it’s a critical component in circuit design, influencing system efficiency, cleanliness, and reliability. While its role may seem straightforward, the way a reservoir is designed, implemented and maintained can have a significant impact on overall performance.
This guide explores how reservoir layout, breather function and fluid contamination control work together to protect your system and prevent costly failures.
Learn moreTop Tips for Safe Hydraulic Cylinder Storage
Hydraulic cylinders are precision components—and storing them properly is just as important as installing them. Rust, seal damage, and fluid contamination can all occur if precautions aren’t taken.
This guide outlines key storage considerations to help you protect your cylinders, reduce risk, and ensure they’re ready for reliable performance when you need them. Because when it comes to hydraulics, prevention is always better than cure. Fact.
Learn MoreAdvantages of Helical Hydraulic Actuators in Heavy-duty Applications
Hydraulic actuators convert pressurised fluid into motion -powering equipment to move, lift, rotate and slide. Depending on the application, designers choose between linear and rotary styles.
This guide explores why helical rotary actuators are often the preferred choice in heavy-duty environments, offering high torque, compact design, and exceptional durability under extreme conditions.
Learn More