A hydraulic motor converts flow and fluid pressure into rotary motion. It’s the muscle of the hydraulic system.
Before we begin looking at different types of hydraulic motors, it is worth reminding ourselves how hydraulic systems work and the role that a hydraulic motor plays within the overall system.
What is the purpose of a hydraulic motor?
Hydraulic systems are designed to transmit power, in a controlled way, through the use of pressurised liquids. Within a hydraulic system, the hydraulic pump ensures the continued flow of fluid. Pressure can then be created by the careful design of applied forces and the gauge of pipes. The hydraulic motor then converts the kinetic energy of flow and the fluid pressure into rotary motion. The amount of oil supplied by the hydraulic pump determines the speed of a hydraulic motor. Subsequently, the torque is dependent on the amount of pressure supplied.
There are many different types of hydraulic motor. Most of them can be categorised as: axial piston motors, radial piston motors, hydraulic gear motors or hydraulic vane motors.
You can learn more about hydraulic motors via the fantastic online content at LunchBox Sessions. Their bite-sized training sessions are packed with interactive learning materials for paying members. But each session includes some free taster materials available to all. It’s a fantastic online resource if you want to know more about how hydraulics and other industrial technologies work.
LunchBox Sessions have kindly allowed us to reproduce some of their e-learning content here.
About hydraulic motors
It can be a little confusing to those new to hydraulic systems when we talk about hydraulic motors. They should not be confused with the “prime mover” – the engine that initiates the process by powering the pump. For this reason, you will also hear hydraulic motors referred to as rotary actuators, since this more accurately describes the function they fulfil within the hydraulic system.
There are two different types of actuators in a hydraulic system: rotary actuators (or hydraulic motors) and linear actuators (or cylinders).
There are also semi-rotary actuators like helical, rack and pinion, and vane actuators, illustrated left to right in the image here.
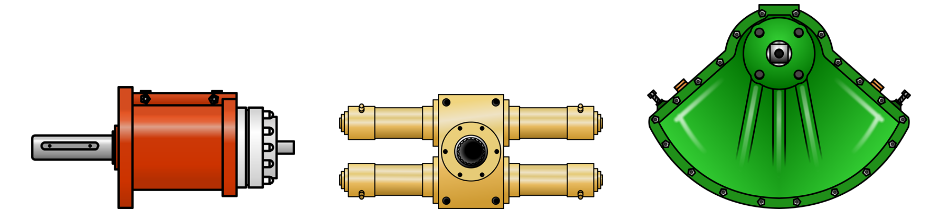
How to choose the right hydraulic motor
Deciding which hydraulic motor is right for your application will depend on a number of factors including:
- Speed
- Torque
- Range
- Physical characteristics such as robustness, weight, size, etc.
- Ease of service / maintenance
- Acceptable noise levels
- Compatibility with the other components in your hydraulic system
Different types of hydraulic motors have different characteristics and will therefore suit different applications. We go into more detail about this in our ultimate guide to hydraulic motors, which explains the differences between:
- Radial piston motors (crankshaft / multi-lobe cam ring design / dual displacement / compact)
- Hydraulic gear motors
- Hydraulic vane motors
- Axial piston motors
- Gerotor motors
Learn about radial piston motors
Radial piston motors are highly efficient and generally have a long life. Furthermore, they provide high torque at relatively low shaft speeds, as well as excellent low speed operation with high efficiency. The low output speed means that, in many cases, a gearbox is not necessary.
Radial piston motors are often referred to as LSHT – Low Speed High Torque motors. We supply radial piston motors from brands worldwide, including Bosch Rexroth, Staffa (Kawasaki) and the Italgroup.
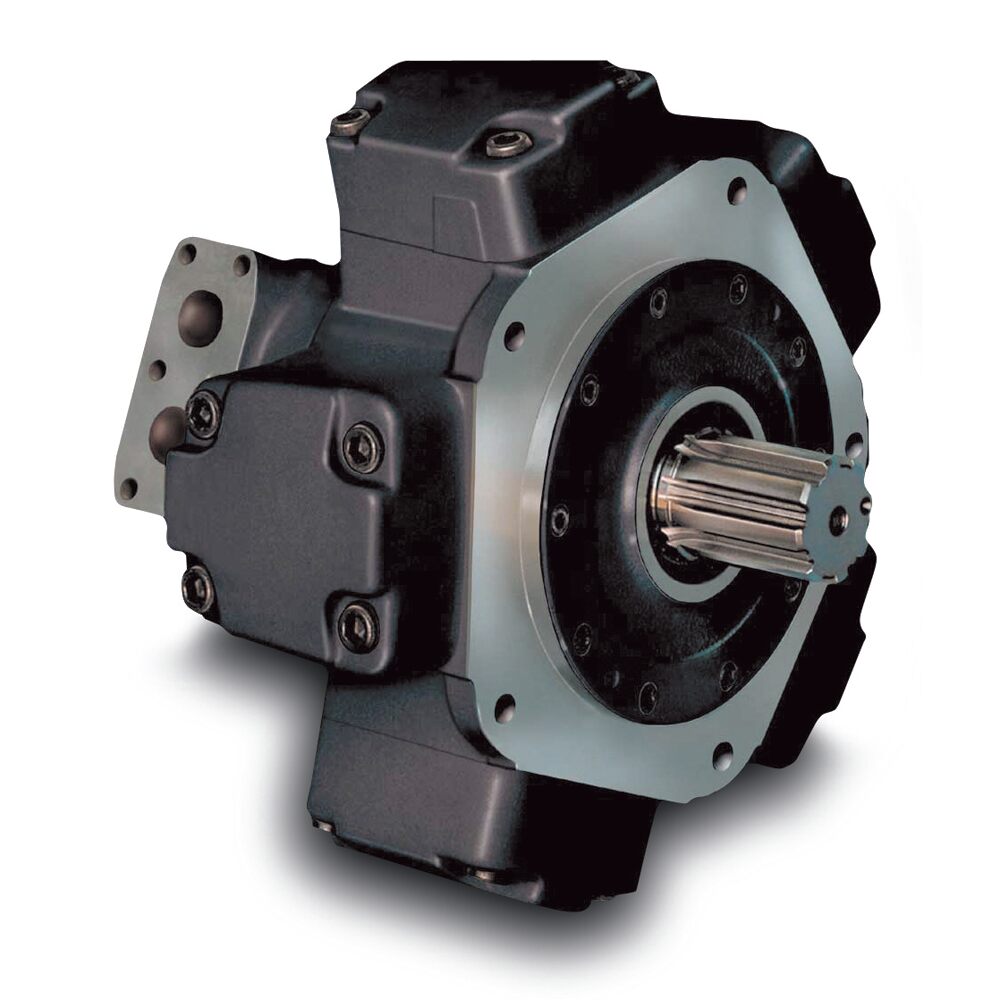
Which applications are radial piston motors commonly found in?
Radial piston motors are commonly fund in: excavators, cranes, ground drilling equipment, winch drives, concrete mixers, trawlers and plastic injection moulding machines.
Which types of radial piston motors are there?
Generally, there are two basic types of radial piston motors. These are explained further here.
Crankshaft radial piston motor
The Crankshaft radial piston motor has a single cam and pistons pushing inwards. Moreover, it has an extremely high starting torque and is available in single displacements from 40 cc /rev through to about 5400 cc/rev. In addition, the Crankshaft type radial piston motors can run at “creep” speeds. And, some can run seamlessly up to 1500 rpm with virtually constant output torque. To sum up, the Crankshaft radial piston motor is the most versatile hydraulic motor.
Multilobe cam ring design
This type of radial piston motor is constructed with a cam ring, which has multiple lobes and piston rollers that push outwardly against the cam ring. In essence, this produces a very smooth output with high starting torque. However, they are often limited in the upper speed range. Moreover, these high power motors are particularly good on low speed applications.
Other types of radial piston motors include: compact radial piston motors, dual displacement radial piston motors and fixed displacement radial piston motors. And in addition, we can also help you source: low speed high torque radial piston motors, two speed radial piston motors and variable displacement radial piston motors.
How do hydraulic gear motors work?
Gears are used to reduce the shaft output speed for applications that require a lower speed. This means that the gear motor’s operating pressure typically is very low, ranging between 100 and 150 bar. In addition, some of the more modern gear motors operate at, up to, 250 bar continuous pressure. However, the downside is that this motor can be rather noisy.
To sum up, gear motors are generally lightweight and small units with relatively high pressures. In addition they are known for their low cost, variety of speeds, broad temperature range, simple design and large viscosity range.
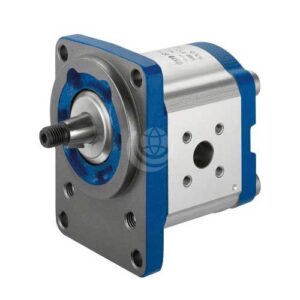
About hydraulic vane motors
Hydraulic vane motors are used in both industrial and mobile applications. For example, screw-drive, injection moulding and agricultural machinery. These motors tend to have less internal leaking than a gear motor. And subsequently, they are better to use in applications requiring lower speeds.
Hydraulic vane motors feature reduced noise level, low flow pulsation, high torque at low speeds and a simple design. Moreover they are easy to service and suitable for vertical installation. To function correctly, the rotor vanes must be pressed against the inside of the motor housing. This can be done through spiral or leaf springs. But rods are also suitable.
A vane motor typically features a displacement volume between 9 cc/rev to 214 cc/rev and a maximum 230 bar pressure. The speeds range from 100 to 2,500 rpm. Maximum torque of up to 650 Nm.
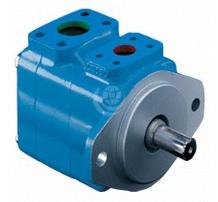
Learn more about axial piston motors
Axial piston motors use a bent axis design or a swash plate principle. The fixed displacement type works as a hydraulic motor and can be used in open and closed circuits. In contrast to this, the variable displacement type operates like a hydraulic pump.
In the bent axis design, pistons move to and fro within the cylinder block bores. This movement is converted into rotary movement via the piston ball joint at the driving flange. In the swash plate design, pistons move to and fro in the cylinder block. Subsequently it revolves and turns the drive shaft via the connected cotter pin.
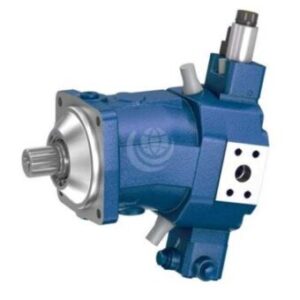
What are the main characteristics of a gerotor motor?
Low speed, high torque (LSHT) hydraulic Gerotor motors feature a high starting torque and large range of speeds with a continuous output torque. In addition, the motor has a good power-to-weight ratio and a smooth operation, even at low speeds. The Gerotor motor’s design is furthermore very robust and built for harsh working conditions.
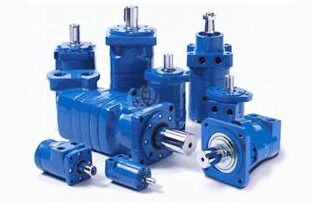
The benefits of using a hydraulic motor
LunchBox Sessions looks at how a hydraulic motor works in order to explain their advantages. Using an industrial construction vehicle to illustrate a typical hydraulic application, it shows how the vehicle’s diesel engine converts the chemical energy of the fuel into rotational energy.
The hydraulic pump then converts the rotational energy into a combination of kinetic and potential energy. Then the hydraulic motor converts the kinetic / potential energy back into rotational energy.
Why are these energy conversions important? Because it makes for greater control and, since most rotary actuators are designed to be bi-directional, it means that reverse motion is possible.
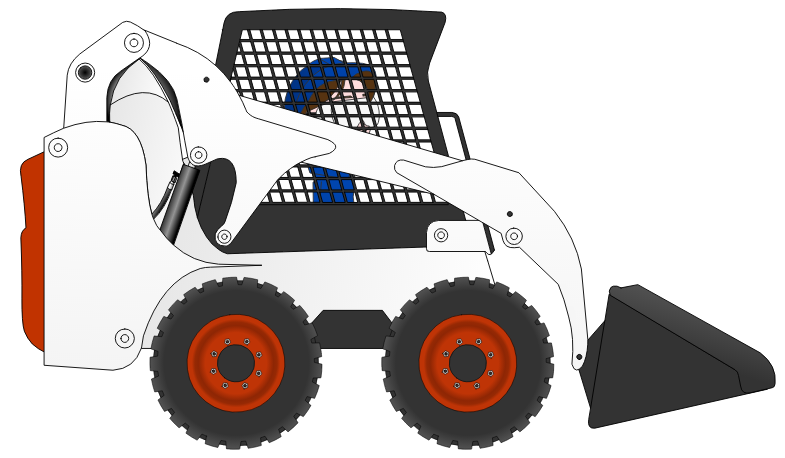
If you would like to learn more about different types of hydraulic motors, you can review LunchBox Sessions’ training on hydraulic motors here. Some of their learning materials are free; you don’t need to sign up. However, if you are serious about expanding your knowledge of hydraulic systems, we recommend you consider signing up for a subscription to the entire LunchBox Sessions service. This way, you get full access to all the interactive training materials, tests and simulations for just $29 per month. Students are entitled to a 60% discount off this price when they share their college or university ID.
Alternatively, as a leading global supplier of hydraulic equipment offering the widest selection of hydraulic brands in the UK, you can view our selection of hydraulic motors here. We only showcase a small selection of the hydraulic motors that we can supply, so please do not hesitate to contact our friendly team for personal service and advice.
We are the first choice for customers in over 130 countries worldwide, supplying a vast selection of hydraulic brands and components.
You are guaranteed impartial, technical advice and optimal solutions. Every time.
Hydraulic Motor Glossary
MOTOR DISPLACEMENT:
BREAKAWAY TORQUE:
MECHANICAL EFFICIENCY:
This is the ratio of actual torque delivered to theoretical torque.
MOTOR SPEED:
TORQUE RIPPLE:
TORQUE OUTPUT:
MAXIMUM MOTOR SPEED:
MINIMUM MOTOR SPEED:
SLIPPAGE:
For the definitions to more hydraulics words, phrases and technical jargon, check out our Ultimate Hydraulics Glossary
Frequently asked Questions and Answers about Hydraulic Motors
Which hydraulic motor brands do you provide?
We have direct access to over 80 leading hydraulic brands. This means that we offer agile and flexible solutions to suit every customer’s budget, lead-time and specifications. Our bestselling brands include: Bosch Rexroth motors, Danfoss motors, Eaton Char-Lynn motors, Italgroup Radial Piston motors, Parker Hannifin motors and Vivolo Vivoil motors.
Our team will work closely with you to advise on the best hydraulic motor for your system and application.
Can you get hold of the exact same motor that we’re already using?
Yes, if you have the manufacturer’s name and product number, we can source any motor still listed in the market. Furthermore, if the motor is now obsolete, our skilled team can source direct equivalents. In some instances, this means better lead-times and reduced cost.
Do you manufacture custom-made hydraulic motors?
We do not manufacture our own motors. However, we have excellent relationships and direct access to 80 leading hydraulic brands. This means that we can source a hydraulic motor, which meets your exact requirements. In addition, we can help with in-house bespoke cylinders or bespoke power pack builds.
Do you ship worldwide?
Yes! Today we export to 130 countries worldwide and are, in the UK, viewed as the hydraulics solutions “gateway” to the rest of the world. Moreover, in 2019, the UK’s Department for Business and Trade appointed Hydraulics Online as a Northern Powerhouse Export Champion. If it’s hydraulic we can design it, supply it, solve it, repair it – and ship it worldwide!
Do you repair motors?
Yes, we repair piston motors and vane motors. Our technical engineers can give a full diagnosis and will contact you to discuss all options available. More importantly, they can identify the best solution for your specific needs. And if applicable, our team offers recommendations on how to future-proof your motor’s performance. Above all, this saves costs and prevents further system downtime.
We’re a hydraulics ‘hub’, offering thousands of possibilities… how can we help?
Explore our other collaborations with Lunchbox Sessions…
An Introduction to Hydraulic Pressure and Flow
An understanding of the key principles of fluid dynamics is, essential for anyone who wishes to build or maintain hydraulic systems.
One of the first concepts that must be understood is how physicists quantify the movement of fluids, namely flow.
Learn MoreDiagnosing Problems Using Pressure Readings
Effective troubleshooting of problems in hydraulic systems requires a good understanding of flow and pressure readings.
In this article, we’re going to look at how pressure and flow can vary depending on the type of hydraulic system and what implications this has for hydraulic system troubleshooting.
Learn moreTroubleshooting Hydraulic Systems: the Reservoir, Breather and Fluid Contaminants
The hydraulic reservoir plays an important part in hydraulic circuit design – storing hydraulic fluid when it isn’t being pushed through the hydraulic system.
While a “fluid storage tank” might seem like a very simple concept, the design and implementation of the reservoir is very important.
Learn more